For the simulation of aerodynamics and aeroelasticity we use CFD methods based on RANS as well as hybrid RANS / LES methods in combination with different structure solvers, whereby the CFD computation chain is successively extended for applications in the wind energy sector. In addition to the numerical study of complex interactions, technologies for passive and active load reduction are developed and evaluated.
Furthermore, the working group has a long tradition in aeroacoustics studies of wind turbines and in the development of noise reduction methods. The working group cooperates with various wind turbine manufacturers and offers support in the investigation of complex aerodynamic effects as well as in design tasks. This includes in particular the development of aerodynamically and aeroacoustically optimized rotor blade profiles.
Lighthouse simulation
During operation, a wind turbine is controlled by various very complex control laws, which are intended to optimise performance and protect against extreme events. In particular, the intervention of the controller in the event of an extreme meteorological event, such as a rapid change in wind direction or speed, must be tested simulatively before damage can occur to the wind turbine in the field. The video was created as part of the IndianaWind research project.
The video was created as part of the BMWK-funded IndianaWind research project.
Our main research focus is on rotor aerodynamics and rotor acoustics of wind turbines.
Rotor Aerodynamics
The investigation of the aerodynamics of a wind turbine is not only important for the determination of power, but also for the determination of loads and load fluctuations. As the size and power of wind turbines continues to increase, measurements are often not possible or too expensive. Therefore, numerical methods are used to investigate the aerodynamic properties of wind turbines. For this reason, IAG has developed a highly accurate CFD-based process chain. This consists of a grid generator, which enables a script-based, automated networking of the geometry, the block-structured CFD code FLOWer from DLR (Deutsches Zentrum für Luft- und Raumfahrt - German Aerospace Center), which is continuously developed and used in the working group for wind energy applications. To measure aeroelastic effects, a time-true coupling with a multi-body simulation program and with an FEM solver was implemented.
The atmospheric boundary layer has a considerable influence on the rotor loads. Therefore, the CFD code in use was extended with a unsteady inflow boundary condition. This boundary condition allows the simulation of unsteady atmospheric boundary layers. Thus it is possible to simulate wind turbines under realistic atmospheric conditions (wind speeds, density and turbulence) and to calculate the interaction between the atmospheric boundary layer including dissolved turbulence and the turbine as well as its wake. The influence of complex terrain orographies or vegetation on the inflow conditions of the plant can also be recorded.
There is an increasing interest in the numerical simulation of transient aerodynamic effects and the calculation of the interaction of the wake with the turbulent atmospheric boundary layer to determine the influence on the inflow conditions for downstream installations, loads and load fluctuations. For this purpose, the wake is finely resolved and calculated using higher-order methods.
The aerodynamic properties of a rotor blade and thus the performance of a wind turbine are decisively determined by the design of the profile sections.
The IAG has many years of experience in the aerodynamic and acoustic design of profiles for wind energy applications as well as the evaluation of profiles. The profiles are developed specifically for the individual requirements of the turbine under consideration. A verification of the theoretical results is possible for the subsonic area in the Laminar Wind Tunnel of the institute, which has an exceptionally low turbulence degree. In addition to polar, pressure distribution and boundary layer measurements, measurements of the trailing edge noise using the so-called CPV method are possible in this tunnel. The extensive experimental investigations carried out there contribute to the further development of the profile design and analysis methods.
- Analysis, design and numerical optimization of profiles
- Aeroacoustic design of "quiet profiles"
- Process development
- Boundary-layer methods, envelope determination, modelling of laminar release bubbles
- Noise prediction models
- Optimization processes
- Wind tunnel measurement of profiles
- Construction of wind tunnel models
- Aerodynamic measurements (polar, boundary layer and pressure distribution measurements)
- Aeroacoustic measurements
Rotor Acoustics
At the Institute of Aerodynamics and Gas Dynamics at the University of Stuttgart different models for the efficient calculation of the trailing edge noise were developed (Xnoise, XEnoise and Rnoise). The calculation results of these models were validated with measurements from the Institute's laminar wind tunnel to qualify them for acoustic analysis and the design of low-noise profiles. The above models are implemented in IAGNoise, which has a graphical user interface. IAGNoise has also been extended for use on 3D geometries. The rotor blade is divided into several 2D profile sections. The total noise of the plant is then determined by adding up the proportions of the individual 2D sections, taking into account the Doppler effect for given observer positions.
The IAG investigates the potential of active and passive measures to reduce the flow-induced noise of wind turbine rotors. The noise reduction achieved can contribute to an increase in the acceptance of on-shore turbines and can be used to increase the performance of future wind turbines by increasing the possible rotor speed. The work in this area concentrates on the reduction of trailing edge noise induced by the boundary layer, which is the dominant noise source. Passive (profile design, rear edge modification) and active measures (suction, blow-out) are used. Among other things, it was shown that a considerable noise reduction can be achieved by constant, flat extraction. Both numerical and experimental studies in this field are carried out at the IAG.
Noise generation is an important aspect in the development of on-shore wind turbines. The resulting noise impairs the acceptance of wind turbines by the population. The strict noise protection regulations demand serious efforts by manufacturers to reduce noise. The flow-induced noise is difficult to calculate and reduce. An important noise component with regard to approval is the so-called rear edge noise. This is caused by the interaction of pressure fluctuations in the boundary layer with the trailing edge of the rotor blades. The pressure fluctuations in turn are caused by turbulent structures in the boundary layer. Since the condition of the turbulence near the trailing edge is determined by the development of the boundary layer and thus by the shape of the pressure distribution in the profile section, it is obvious that the trailing edge noise can be reduced by an adequate profile design. The aim is to reduce the noise while increasing the aerodynamic performance at the same time.
Based on extensive experience in aerodynamics and aeroacoustics of profiles, the IAG analyses profiles using its own acoustic models with regard to the identification of potential noise sources and the simultaneous development of measures for their reduction.
Dr.-Ing. Thorsten Lutz
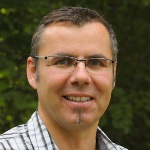
Thorsten Lutz
Dr.-Ing.Head of working group Aircraft Aerodynamics / Head of working group Wind Energy